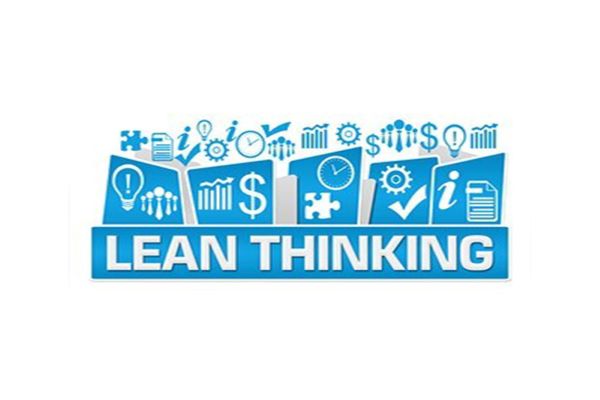
As we noted in a previous post on the ‘8 Wastes’ in business, the ideas behind ‘Lean Thinking’ originated in the manufacturing industry. However, every business contains ‘waste’ – areas where time or money is being misused – which means that the concepts are applicable to almost any type of business.
Lean Thinking helps your company create efficiencies and become more effective while helping you deliver high-quality products or services. This process involves:
- Identifying activities that create value for customers
- Determining the sequence of those activities
- Eliminating activities/steps of the process that do not add value
- Letting customers dictate ‘pull’ and demand
- Improving the process and evaluating results
If you haven’t applied these concepts to your business yet (or need a little more convincing), here are 6 reasons why Lean Thinking isn’t just for manufacturing companies:
- Every industry has repeatable processes
Whether it’s invoicing, packing, shipping or taking orders from customers, there are things your team does over and over again. Chances are, there’s room for improvement, a way to eliminate extra steps or speed things up. - Customers expect and are willing to pay for high-quality products, service or advice
Ultimately, Lean Thinking focuses on creating value for customers. When customers get what they asked for and paid for (value) they’ll come back for more. - Non-manufacturing environments have lots of hidden wastes within their processes
‘Lean’ is about finding better ways to do things and continually evaluating processes and performance to see where they are weak. Every business can seek out better ways to get work done and use less effort, less time and fewer resources. - Rework and waiting are the two main wastes observed in processes
Within the 8 Wastes, ‘waiting’ includes things like waiting for an email response, waiting for a review, or waiting for materials to arrive. ‘Rework’ involves having to re-do tasks or services (eg. correcting problems due to poor quality, fixing a mistake, etc.). You can almost certainly identify areas of waste or rework in your business that could be eliminated or improved! - Effective resource allocation can significantly improve your service delivery
Resource allocation involves allocating budget, equipment/tools, people and information to the areas where they’re needed most. By cutting out waste, you’ll be able to gather the right information more quickly, make faster decisions, improve resource allocation and your delivery to customers. - Lean Thinking is the roadmap to cultural transformation through education, empowerment and ownership
In order to ‘get leaner’, a company has to acknowledge that there is a need for change and improvement, and this requires focus and input from all team members. Implementing Lean Thinking, then, builds teamwork, cooperation and a level of investment from staff.